Working in construction involves a risky environment where employees encounter multiple potential risks that may result in injuries or fatalities. The United States construction industry contributed to nineteen percent of total workplace fatalities in 2022 based on statistics showing 38.4% of these fatalities were due to falls, slips, and trips.
Workplace fatalities statistics confirm the importance of construction safety management standards as a standardized approach to detect and examine technological hazards and minimize their impact on workplace safety for protected working areas. Safety management safeguards workers through its implementation while ensuring both project performance and regulatory compliance.
Understanding Construction Safety Management
Construction safety management utilizes developed policies and procedures that create prevention measures against construction site injuries and accidents. All risk elements and their assessment need proper identification, followed by employee training and continuous monitoring within an integrated safety management system. Safety management systems must run through every developmental stage of projects from design to finish to help construction companies prevent workplace dangers and protect their workers’ safety.
Why is Construction Safety Management Important?
Reduced Accident Rates
Safety management programs significantly reduce work-related accidents. The three most frequent construction site accidents are falls, slips, and trips. Employee protection relies on two factors: adherence to safety protocols and suitable training implementation by companies.
Worker Protection
The fundamental safety management principle requires complete dedication to protecting employees from risks. Employee safety in a secure workplace environment upholds their health, improves workplace morale, and increases productivity. Worker safety operations create optimal performance, which leads to project success.
Legal and Financial Implications
A lack of proper safety measures can lead to legal action, higher insurance costs, and monetary fines. OSHA (Occupational Safety and Health Administration) enforces requirements to establish safe working environments for all employees. Non-compliance can cause a company severe financial consequences and reputational harm. Making safety management investments is wise because of its obvious business benefits.
Industry Reputation and Accountability
An organization with good safety performance continues to build its professional standing among industry peers. Companies focused on worker safety gain partners and clients who regard them as dependable organizations with solid reputations. When customers develop favorable views about a company, their chances for new business opportunities and sustaining long-term success improve.
Economic Efficiency
Projects experience delays when accidents or injuries occur because such events lead to elevated expenses and the departure of trained personnel. A strong safety management system prevents accidents, helping businesses preserve their project schedules and budgetary targets for better financial efficiency.
Compliance with Regulations
Obeying safety regulations is a legal obligation that is not optional for any construction industry. Construction companies need to fulfill all OSHA standards that protect worker safety. Following safety standards avoids legal trouble while establishing companies that value ethical operations.
Common Hazards in Construction
Safety management must focus on understanding standard workplace risks because it leads to effective protection processes. Some prevalent dangers include:
- Falls: The most significant cause of fatalities in construction sites is mainly because workers lack proper fall prevention systems.
- Struck-by Incidents: Workers are struck by moving equipment or objects and get injured badly.
- Electrocution: Workers by mistake touches wires containing electricity or faulty electrical equipment.
- Caught-in/between Accidents: Workers become caught and compressed when equipment or structures press against them.
- Exposure to Hazardous Substances: Harmful chemicals and silica dust exposure can lead to respiratory complications in workers on site.
Key Components of an Effective Safety Management Plan
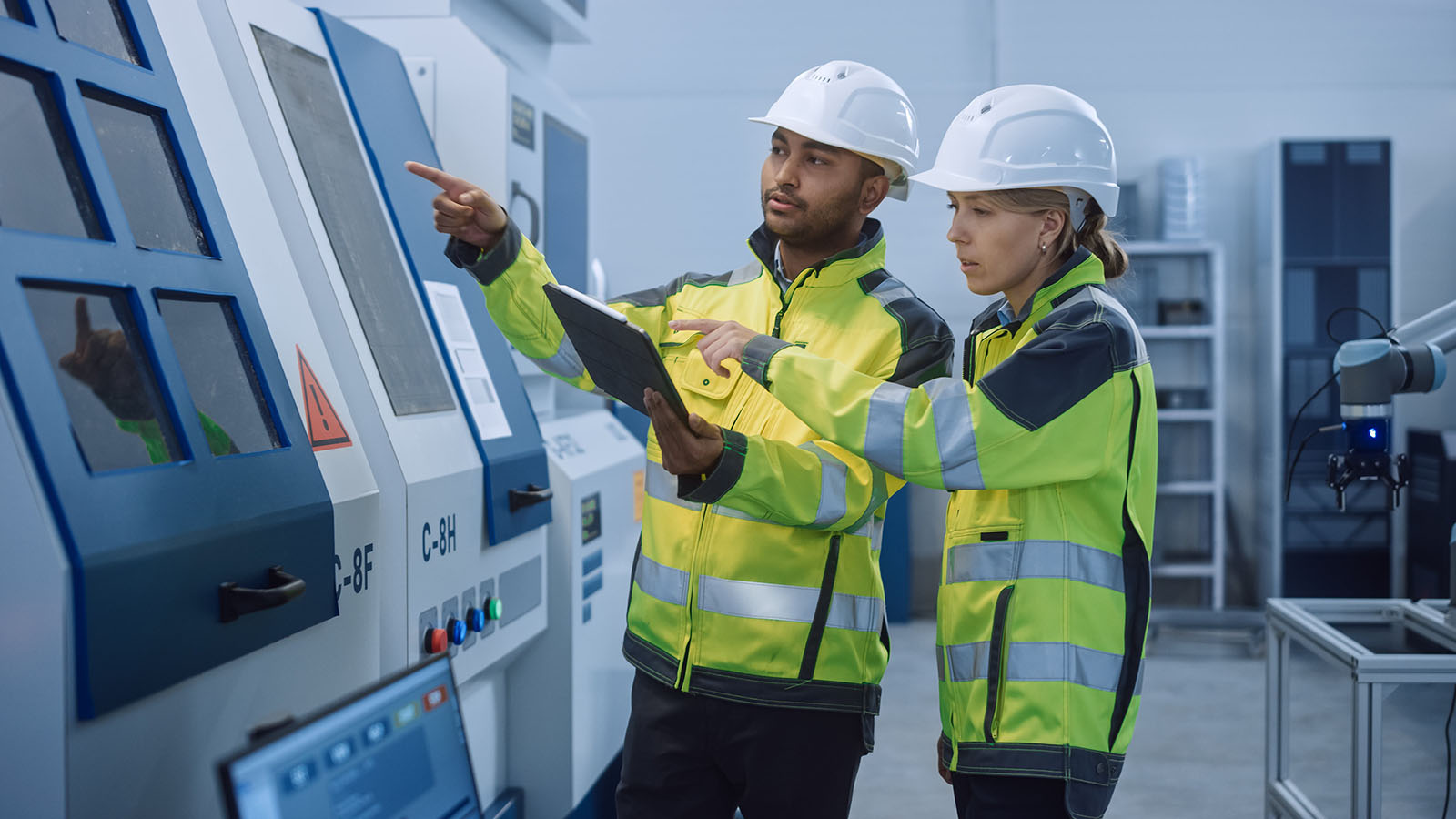
Hazard Identification and Risk Assessment
Safety plans require systematic identification of potential risks and assessment of related hazards at their base. Stakeholders or project managers must perform routine site inspections while conducting job safety assessments and use hazard checklists to find possible dangers in advance.
Safety Policies and Procedures
The organization establishes safety protocols and procedures that define safe operating procedures. These safety guidelines must be documented so employees can easily access and understand them. All the practices that are documented must be practiced and maintain organizational safety.
Training and Education
A constant training program allows employees to recognize potential dangers and master secure operational methods. A safety training program for new employees must include recurring meetings and exclusive training for particular equipment or task operations. Instructional programs help workers notice dangers in their surroundings and avoid dangerous situations, promoting a secure workplace.
Personal Protective Equipment (PPE)
The proper distribution of PPE, including helmets, gloves, safety glasses, and harnesses, protects workers from injuries. Safety management requires immediate access to PPE, combined with proper maintenance and effective learning by workers on how to use it properly.
Emergency Preparedness
Even after taking several preventive steps, emergencies can occur anytime. Therefore, a detailed emergency response plan that incorporates evacuation procedures, first-aid stations, and communication protocols must be developed. The emergency plan’s regular drills and frequent updates create organizational preparedness, leading to lower consequences during emergency situations.
Conclusion
All construction sites require focused attention to safety management as an essential industry function. Construction safety management involves safeguarding workers, meeting legal standards, and achieving better project results. Safer workplaces are created when companies understand the importance of safety, identify workplace hazards, and develop complete safety management frameworks. Accident prevention and safety culture enhancement result in workplace morale advancement, increased productivity, and positive reputation growth in the industrial sector.
OnIndus provides construction companies and government agencies with safety-driven technological solutions integrated into Project Management Information Systems (PMIS). It uses expert knowledge to enhance compliance capabilities, risk management, and real-time safety tracking systems. Contact our team to learn how we optimize project efficiency while improving safety operations.